Fiber-optic CAN measurement module for temperature measurement
The new, fiber-optic CAN measurement module imc CANSAS-FBG-T8 makes testing in high-voltage environments safer and easier. Thanks to the optical operating method, the measuring point and the instrument are fully decoupled. At eight optical inputs, the module can measure temperatures on arbitrary electrical levels using specially developed sensors with fiber Bragg grating technology (FBG). Data are output via CAN.
At a glance
- 8 channels
- Temperature measurement
- 1 kHz sampling rate
- 100 Hz bandwidth
- CAN output
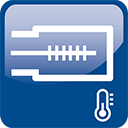
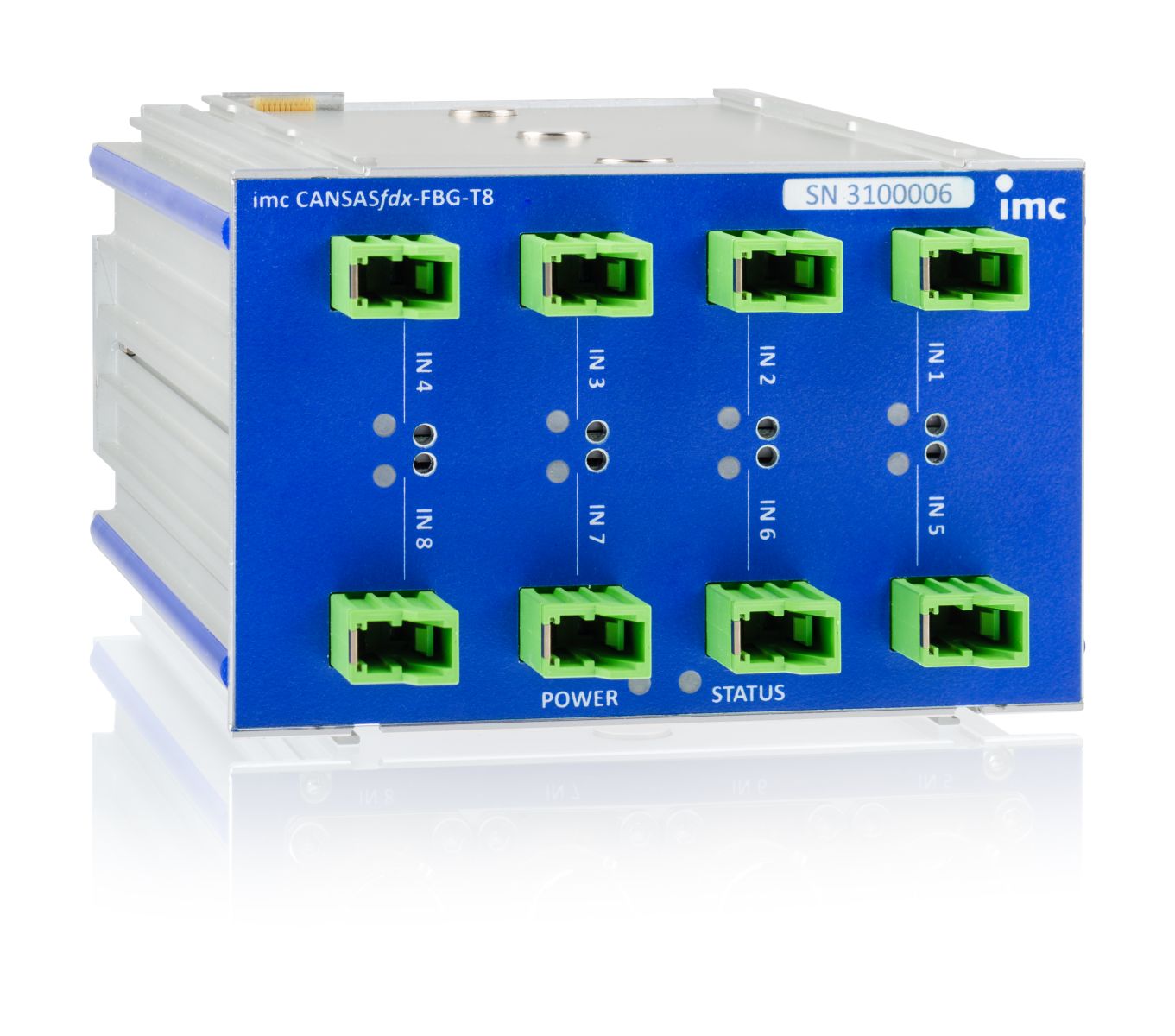
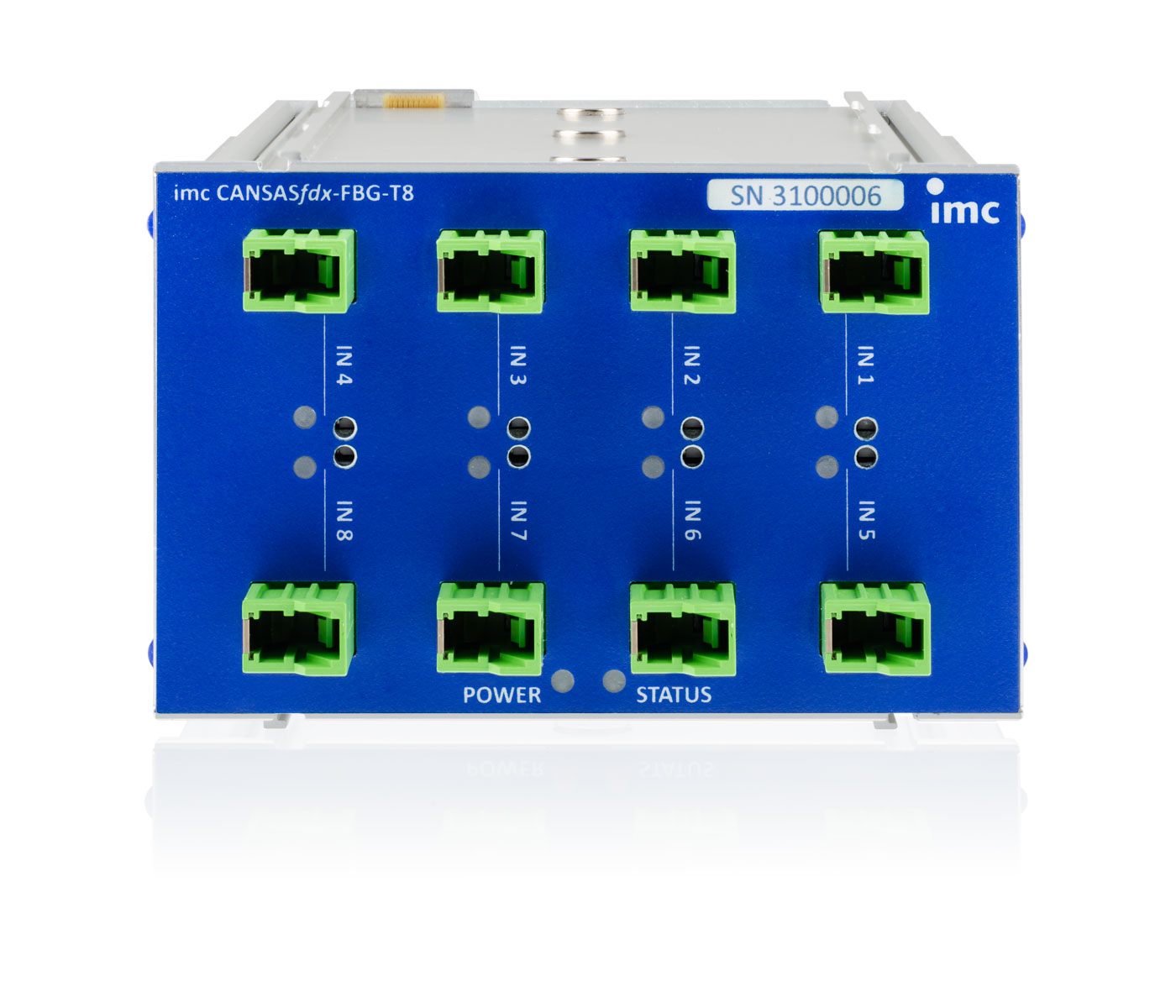

Safe measurement in high-voltage environments
When working at voltages beyond 50V, comprehensive protective measures are mandatory. This also applies to the involved measurement technology, if it is connected electrically. Possible issues with safety at work are substantially alleviated with the fiber-optic measurement technology from imc: The fiber-based sensors have no electrical conductivity whatsoever. Hence, neither safety-related specific equipment nor special training of the operating personnel are necessary. Complex and expensive high-voltage rated cable insulations are also unnecessary.
Clean measurement results despite high-voltage environment
Particularly users performing measurement in high-voltage environments or in the field of electro-mobility benefit from the robustness of fiber-optic technology. Thanks to the optical measurement principle, this technology is immune to electrostatic and electromagnetic interference, which is frequently a problem when using classic measurement technology in high-voltage environments
Easy handling thanks to small cable diameters
While the elaborate and thick high-voltage insulation of electric sensor cables is obsolete, the size of FBG fiber sensor cables is only less than one millimeter in diameter. They therefore require 90% less space than classic high-voltage cables with a diameter of 3-4 mm. An important advantage, particularly for multi-channel measurements with hundreds of sensors. The cable harnesses can be installed more easily and well fit narrow feed-through.
Measuring inside the windings of electric motors
The particularly thin FBG temperature sensors (type „xxs“) have a diameter of only 0.5 mm in their active zone. This makes assembly easier and enables completely new applications. For example, the sensors can be directly inserted into the winding of electric motors without altering the properties of the motor (in particular field characteristics) thanks to their small size. The very fast response of the fiber-optic sensor will then allow to precisely record, the heating of the winding under dynamic load conditions, for instance. A task that could formerly hardly be solved with classic sensor technology (PT100 or thermocouple).
Easy to operate
We have attached great importance to comfortable operation: Simply connect the imc FBG sensor to the module and enter the characteristic data in the imc CANSAS software or directly transfer them s via Drag & Drop from the imc SENSORS database: Measurement can begin.
Easy to integrate
The fiber-optic measurement module can be integrated into any test environment. Via CAN bus interface the data can either be directly forwarded to a data logger, an application system or a test automation environment.
Patented sensor technology
The fiber-optic temperature sensors from imc have been specially developed for use with the CAN measurement module. The patented sensor is based on a single-mode optic fiber with an inscribed fiber Bragg grating ("FBG"), which is integrated in a very thin glass capillary housing with a diameter of less than 1 mm. It therefore reacts extremely quickly and can be installed in the smallest of spaces.
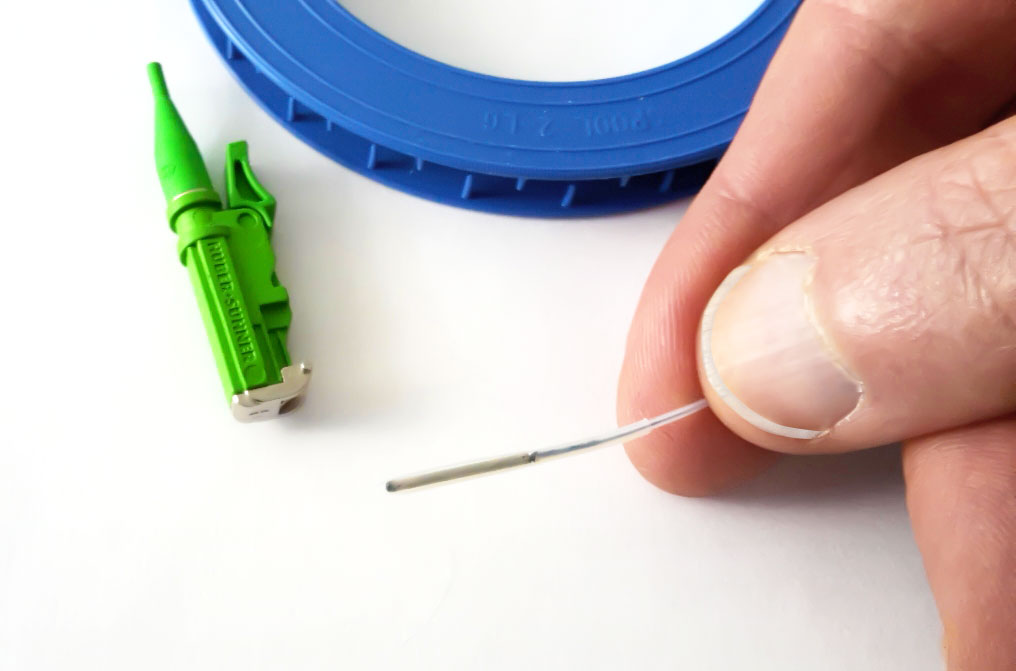
Sensor sizes
imc FBG-temp | xxs | s |
---|---|---|
Properties | very small & fast | particularly robust |
Diameter | 0.5 mm | 1.5 mm |
Response time | 0.2 s | 1.5 s |
Operating range | -40° C ... +220° C |
Convenient handling and connection technology
The FBG sensors from imc are equipped with the robust E2000/APC connector technology. This has an integrated protective cap on the sensor and measuring equipment side, such that the fiber optic is protected against dust and dirt. As soon as the connector is plugged into the socket, the cap opens automatically. A locking mechanism prevents the connector from coming loose accidentally after connection. And if the cable should be too short, then users can extend it at any time by means of a coupling and an optical patch cable.
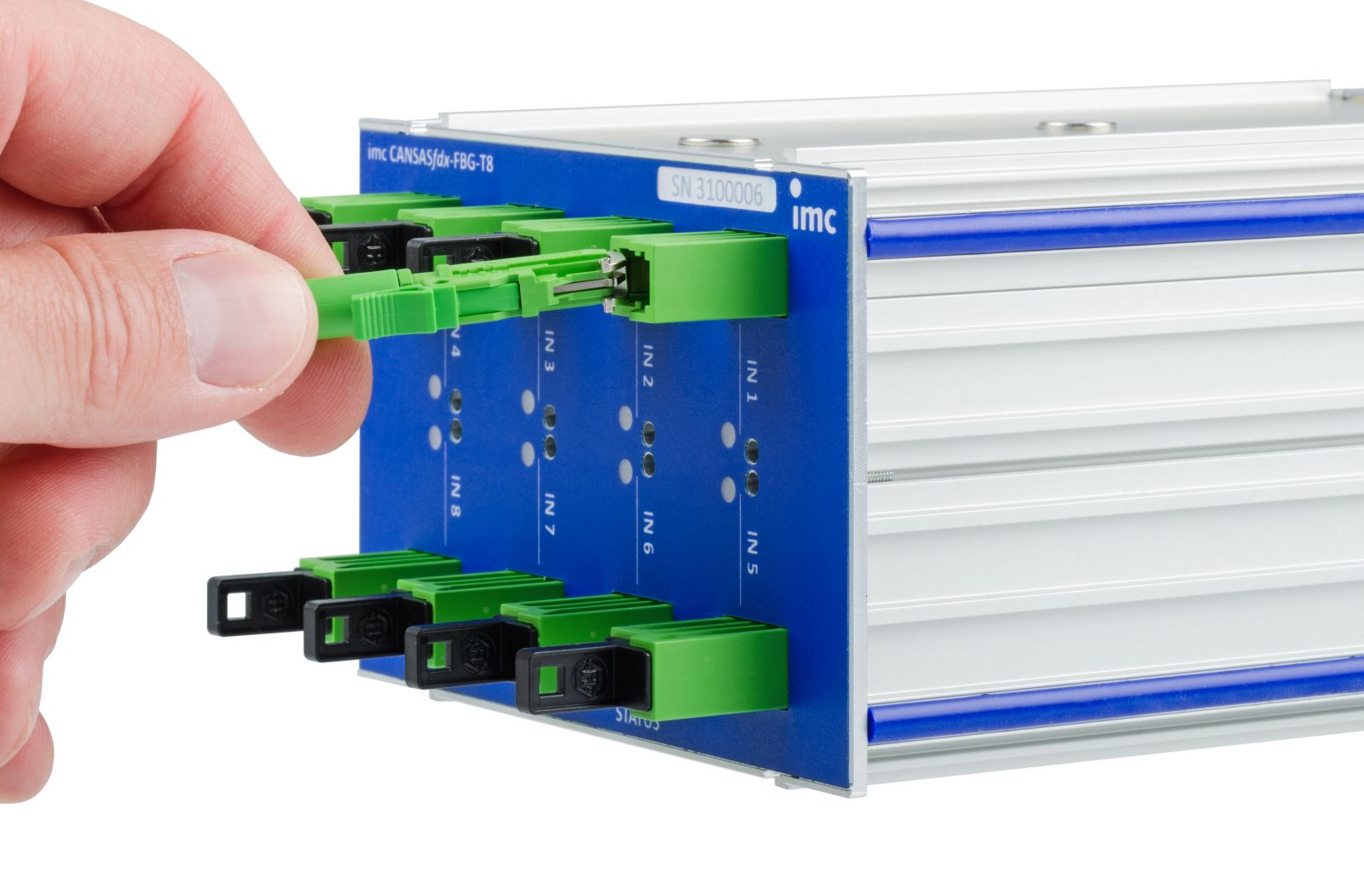
Fiber-optic and electric measurement technology combined
The fiber-optic CAN measurement module is electrically and mechanically compatible with the imc CANSASflex series. This means that it can be connected to any measurement module of the flex series via the integrated click connector. Thus, the entire portfolio of imc‘s classic electric measurement technology is available. This of course also applies to the intelligent CAN data logger imc BUSDAQflex. It can be directly docked (clicked), thus combining any number of fiber-optic and conventional electric measurement modules into one synchronized measurement system. Various measuring, testing and even control applications can be flexibly covered and all major vehicle and industrial buses can be integrated.
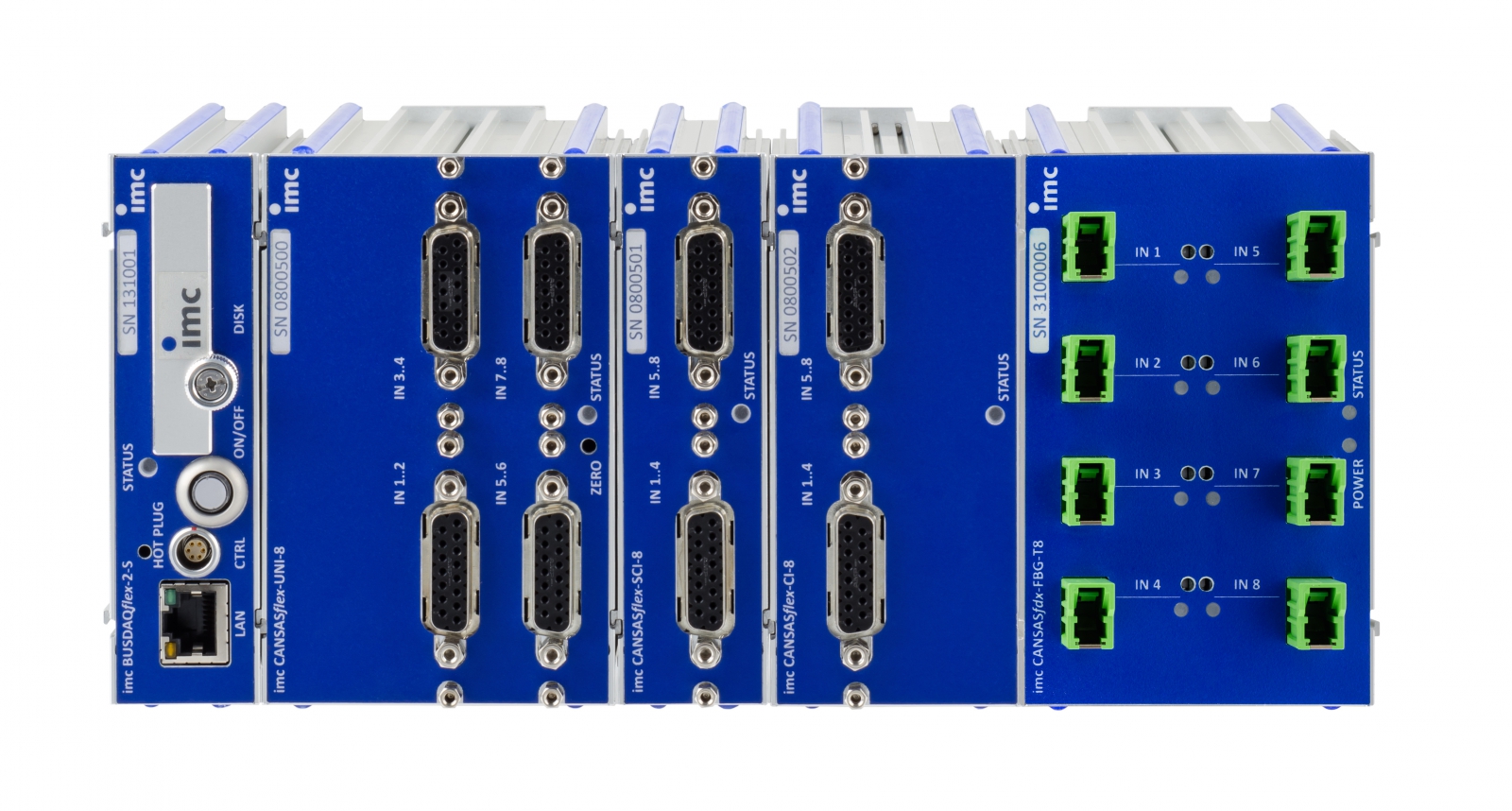
Application examples
Automotive
For applications in the automotive industry, imc offers robust and compact wireless telemetry systems for the non-contact transmission of measurement data for torsion, temperatures, forces and vibrations of rotating parts on vehicles.
Development of electric motors
Modern electric motors are faced with demanding requirements: high torque, long service life, low self-heating. Many tests and measurements are necessary during development to succeed in squaring the circle. Important knowledge is gained if you manage to observe the winding temperature of the motor in active operation.
Such measurements could hardly be accomplished so far with classic high-voltage thermocouples: On the one hand the strong electric and magnetic fields frequently lead to errors in the measurement signals due to EMI and ESD interference. On the other hand the placement of large high-voltage sensor probes alters the winding geometry and distorts the field distribution. This can disturb symmetry and the motors concentricity and even lead to resulting additional noise. Thus, such alterations of the object under test might possibly render the entire test disputable.
However, the 0.5 mm slim FBG sensors can be directly installed in the winding without any mentionable influence. And thanks to the optical measuring method, the signals and results are no longer challenged by electromagnetic interference.
Pantographs on rail-bound vehicles
The pantograph on a train is heavily stressed during operation. The contact strip is in permanent contact with the catenary wire during the journey. The contact strip of the pantograph is made of a softer material to ensure that the catenary wire does not wear too quickly: typically carbon or aluminum alloy is the chosen materials. During travel it is subjected to high thermal stress caused by friction, electric arcing, etc.
With the fiber-optic measurement technology of imc, developers are now able to reliably and precisely record temperatures directly in the carbon brush of the pantograph. Thanks to the fast response behavior of the FBG sensors and the high sampling rate of 1000 Hz, even dynamic temperature curves for electric arcs, burn-off and the like can be examined. The fact that the measurements take place at a level of 15,000 V is only a secondary issue thanks to the fiber-optic technology: Measuring point and data acquisition are electrically decoupled.