High-precision steering effort sensor: The CLS
With the innovative CLSx steering effort sensor, the original steering wheel of your vehicle becomes a high-precision instrument that measures steering torque, angle, steering velocity and acceleration in x, y and z directions. Whether passenger car, truck or construction machinery, the ultra-slim sensor can be placed between the steering column and steering wheel in just a few simple steps. The functionality of the original steering wheel including airbag is completely preserved.
Important features at a glance:
- Detects torque, angle and rotational velocity
- Acceleration measurement in X, Y & Z directions
- World's smallest and lightest sensor
- Optimized for autonomous driving tests
- Quick and easy installation on almost all vehicles
Ideal for the following standards:
- ISO 4138 Steady-state circular driving
- ISO 7975 Braking in a turn
- ISO 7401 Lateral transient response test
- ISO 3888 Severe lane-change maneuver
- ISO 7401 Sinus weave test
- ISO 17288 Free-steer behavior
- ECE-R 79 Steering equipment
- NHTSA Fishhook test (tipping stability)
Data Sheet
Innovative steering sensor for modern tests of ADAS and AD
The innovative CLSx steering effort sensor measures torque, steering angle and velocity with high precision. Additionally, it also acquires acceleration in the center of the steering column (x, y and z direction), as well as rotational acceleration. The CLSx sets new standards in the size of the housing as well as in resolution and accuracy of measurement values.
High-resolution A/D converters with 24 bits ensure especially good signal quality and noise-free results even at small moments below 3 Nm. This is particularly important when testing advanced driver assistance systems (ADAS) and autonomous driving (AD) to determine the overpressure torque. Combined with the innovative design of the sensor housing, this results in a highly accurate steering torque measurement of 0.1% FS (at ±100 Nm). The torsional stiffness of the sensor (without adaptation) is 0.025° at 100 Nm.
Measured variables
- Torque ±100 Nm (others on request)
- Steering angle ±1440° (± 4 revolutions)
- Steering velocity ±2048°/sec
- Acceleration in x, y & z directions
- Rotational acceleration
Award Winner
The CLSx is much smaller than comparable products. In addition, we were able to significantly improve the measuring accuracy of the sensor through the optimized design.
Florian Sailer, Product Manager for Automotive Sensors at imc
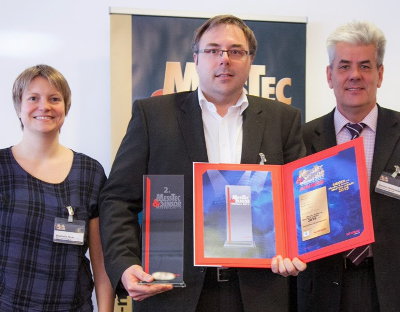
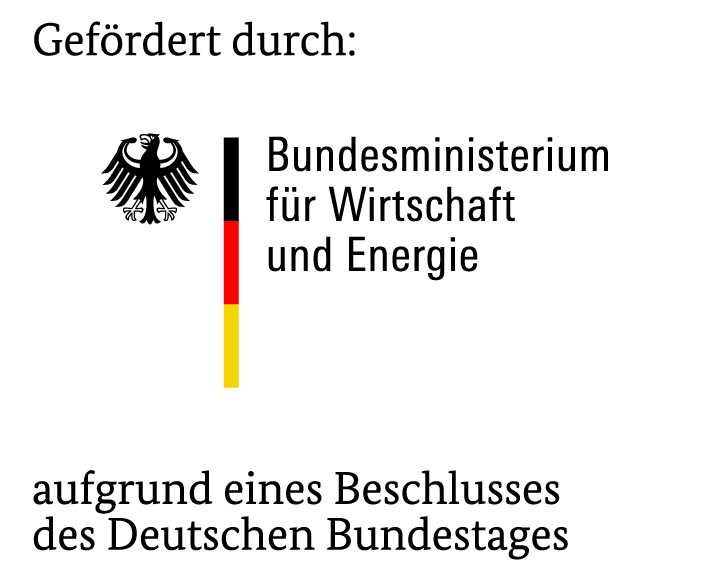
These advantages convinced both the editorial staff of the trade journal messtec drives automation and the specialist audience: The CLSx was awarded the Messtec & Sensor Masters Award in the sensor category.
Comfortable and quick mounting
The CLSx steering effort sensor is mounted between the original steering wheel and the steering column in just a few simple steps. The wiring (LIN bus) of the original wheel is simply routed through the sensor so that all electrical functions and the airbag are retained. With an extremely narrow installation height of 30 mm (without adapter), it extends the steering column only minimally.
Via the CAEMAX adapter systems, which are manufactured according to the vehicle, the steering sensor can be used on almost all vehicle types available worldwide. The ESP functionality of the vehicle is maintained by optionally available adapters for the ESP angle sensor integrated in the vehicle. With short set-up times and convenient software functions, such as remote zeroing for torque and angle of rotation, the system is test ready in a very short time.
Applications
The application possibilities of the steering effort sensor are numerous: from classical tests for the tuning of the steering system in passenger cars to verification measurements for construction machines and validations of autonomous vehicles.
Sub-Section: Accordion for Applications
Steering system setup
The CLSx steering sensor is particularly suitable for use in driving dynamics tests such as:
- ISO 4138 Steady-state circular driving
- ISO 7975 Braking in a turn
- ISO 7401 Lateral transient response test
- ISO 3888 Severe lane-change maneuver
- ISO 7401 Sinus weave test
- ISO 17288 Free-steer behavior
- ECE-R 79 Steering equipment
- NHTSA Fishhook test (tipping stability)
Evaluation of driver assistance systems and autonomous driving
When operating vehicles with driver assistance systems, Advanced Driver Assistance Systems (ADAS) and autonomous driving functions, the following still applies: the driver is responsible and must be able to control his vehicle at all times. This means that steering maneuvers by ADAS systems such as lane keeping and lane change assistants must be able to be influenced manually by the driver at any time. The steering torque required for this - also known as overpressure torque - must not exceed 3 Nm. The CLSx steering sensor is ideal for investigating this overpressure torque, as it delivers high-resolution results even in this small measurement range. The original steering wheel with all functions, including airbag and capacitive hands-off detection, is retained. Due to the very compact size and the low weight, the sensor has a low mass inertia torque. In addition, it operates with particularly low friction. All this ensures that the mounted steering sensor has hardly any influence on the steering system of the production vehicle. The steering behavior thus remains equivalent to that of the production vehicle.
Misuse test for steering systems
In a misuse test, the behavior of a vehicle or a vehicle component is examined in extreme situations - as is the case with steering systems. A test is the sliding along an obstacle with corresponding steering torque and permanent steering angle, for example on a curb.
The CLSx steering sensor can be used to precisely examine the maximum steering torques that can occur. For safety reasons (protection of the test driver), the CLSx steering sensor has a high breaking strength of over 500 Nm.
Comfort measurements
Comfort and handling behavior are tested in continuous operation under realistic driving conditions. An important component is the measurement of steering vibrations in the x, y and z directions. With the integrated MEMS acceleration sensor, the CLSx steering effort sensor measures vibrations in all three spatial axes up to 5 g. In addition, the rotational acceleration up to ±10,000 °/s2 is also measured.
Usability
Thanks to the universal adapter system, the CLSx steering effort sensor can be used to investigate the steering behavior of almost all steering systems in vehicle construction and mechanical engineering sectors:
- Passenger cars and trucks
- Agricultural machinery (tractors, harvesters)
- Road construction machines and special vehicles
- Shipbuilding, watercraft, aviation
- Test benches for steering systems
Technical Data - CLSx
Steering torque
Parameter | Value | Remarks |
---|---|---|
Measuring principle | temperature compensated strain gauge application | |
Measurement range | ±100 Nm | others upon request |
Accuracy | 0.1% FS | Combined (gain error and non-linearity) |
Bandwidth | 0 to 800 Hz | sampling rate 5 kHz |
Steering angle
Parameter | Value | Remarks |
---|---|---|
Measuring principle | incremental angle encoder | |
Measurement range | ±1440 ° | |
Accuracy | 0.045 ° | |
Bandwidth | 0 to 800 Hz | sampling rate 5 kHz |
Steering velocity (angular velocity)
Parameter | Value | Remarks |
---|---|---|
Measuring principle | calculated from angle | |
Measurement range | ±2048 °/s | |
Bandwidth | 0 to 800 Hz | sampling rate 5 kHz |
Vibration and acceleration
Parameter | Value | Remarks |
---|---|---|
Vibration | in the center of the steering column, measurement range up to 5 g in x, y and z direction | |
Rotational acceleration | measurement range ±10000 °/s2 |
General data
Parameter | Value | Remarks |
---|---|---|
Sensor height | approx. 30 mm | without adapter |
Sensor weight | approx. 0.6 kg | without adapter |
Overload | >100% of the measurement range | |
Mech. breaking torque | >500 Nm | |
Adaption | special adaption sets for any car or truck manufacturer available | |
Moment of inertia | approx. 3000 g cm2 typ. approx. 500 g cm2 | |
Working temperature | -20°C to +80°C |
Control unit
Parameter | Value | Remarks |
---|---|---|
Supply | 9 to 36 V DC | |
CAN output | freely configurable | |
Analog output | freely configurable, max. ±10 V | |
Auto zero | with push-button for torque and angle at the panel or by remote control |