Testing safely in high-voltage environments
Automated testing and evaluation of e-vehicle batteries
When developing new batteries and battery management systems for electric vehicles, extensive tests and validations are the order of the day. This includes life cycle testing and misuse tests. These can be used to determine the load limits of battery cells, battery modules and complete battery packs. Investigations include charging and discharging cycles in climatic chambers as well as crash loads, penetration, compression, bending and vibration tests. These comprehensive tests require a flexible, automated test system, including data evaluation. The measurement technology acquires data safely and without disturbance in a high voltage environment. SK Innovation, one of the world's largest battery manufacturers, relied on the HV measurement technology from imc Test & Measurement and commissioned several measurement racks for battery tests.
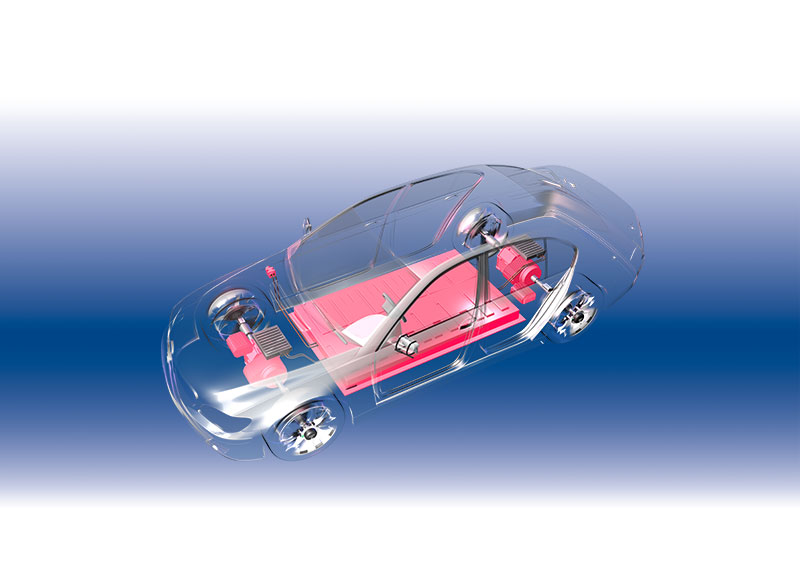
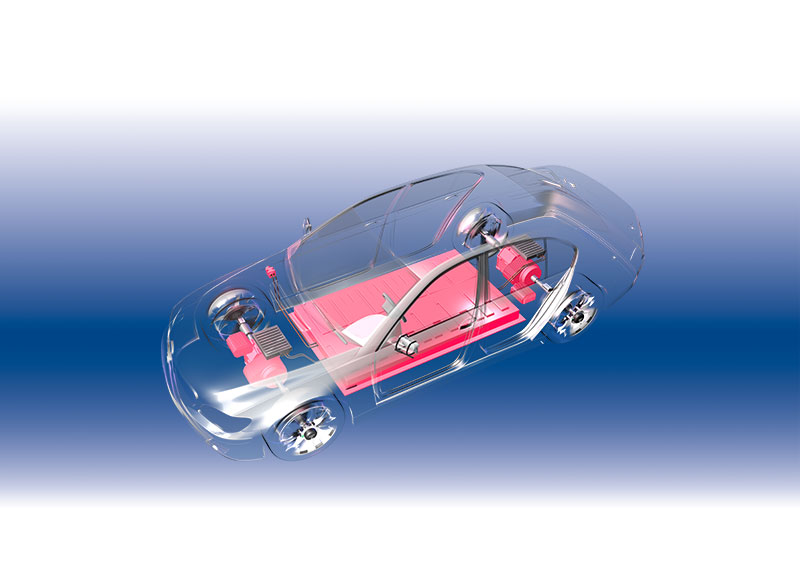
New battery systems for e-vehicles must be safe and reliable. For this reason, extensive tests are carried out in the development phase on individual battery cells, battery mod-ules, and even the entire battery pack under a variety of conditions. Due to the high voltages of a battery of up to 800 V, measurement technology must be highly isolated. This pre-vents electromagnetic disturbance and en-sures the safety of personnel during the test. It is not uncommon to have more than 100 measuring points when measuring tempera-tures and cell voltages with a high voltage po-tential.
imc measurement technology for high-voltage environments
Various highly insulated CAN measurement modules are used in the test racks commis-sioned for the battery test by SK Innovation at imc Korea. Of the seven imc CANSASflex-HISO8-L CAN measurement modules, each of-fers 8 highly isolated inputs for measuring cell voltages and temperatures (PT100 / thermo-couples) up to a voltage level of 800 V (see Fig. 2). In total, up to 56 cell voltages can be meas-ured simultaneously. Twenty-four thermocouples can be operated at a voltage level of 800 V using 3 imc CANSASflex-HISO8-T-8L (Fig. 3) measurement modules. Furthermore, SK Innovation uses 2 imc CANSASflex-SCI16 modules to connect a further 32 thermocouples for temperature measurement. The module voltage is meas-ured with imc CRONOSflex HV4U, which has a measuring range of up to 1000 V.
Highly isolated and safe
Measuring points in the high-voltage range are danger points. In the course of personal safety and occupational health and safety, var-ious measures must be taken to minimize property damage and personal injury or to ex-clude liability issues in the event of a fault. On the one hand, only highly insulated measuring modules may be used; on the other hand, only trained personnel or those who have received additional training may carry out the installa-tion and wiring of the measuring modules. The imc CANSASflex-HISO8 modules used here have a high insulation resistance of 800 V CAT I and 300 V CAT II. The imc CRONOSflex / HV2 modules for direct measurement of 1000V even have an insulation resistance of 1000 V CAT II and 600 V CAT III and thus offer a safe and trouble-free acquisition of measurement data (Device safety standard EN 61010).
Endurance test with the imc test rack
The 19”-test rack captures all measured values on a battery module consisting of several individual battery cells. Cell voltage and temperature are measured and monitored during the test on each bat-tery cell. For this, SK Innovation uses several 19” racks. The test system also acquires the voltage of the battery modules and the entire battery pack. imc STUDIO software also controls and regulates the bidirectional DC source for the charging and dis-charging process and monitors measurement quantities
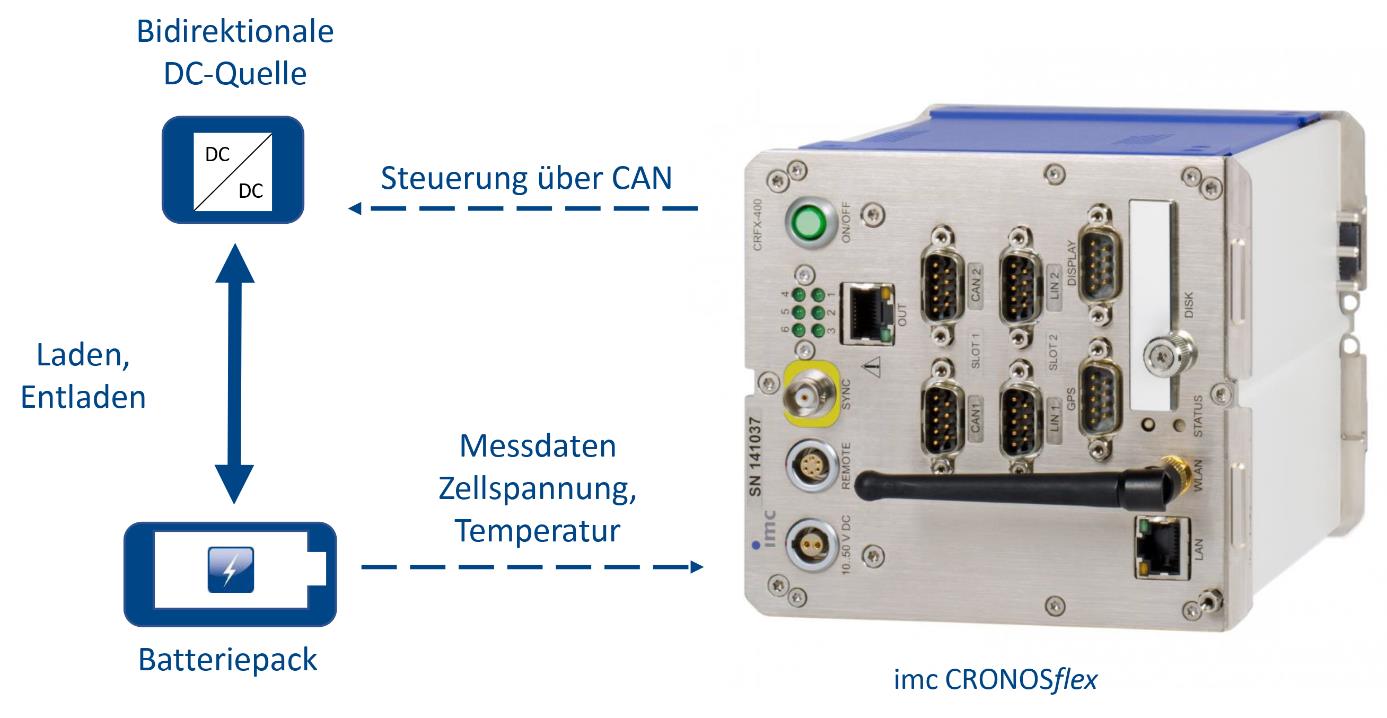
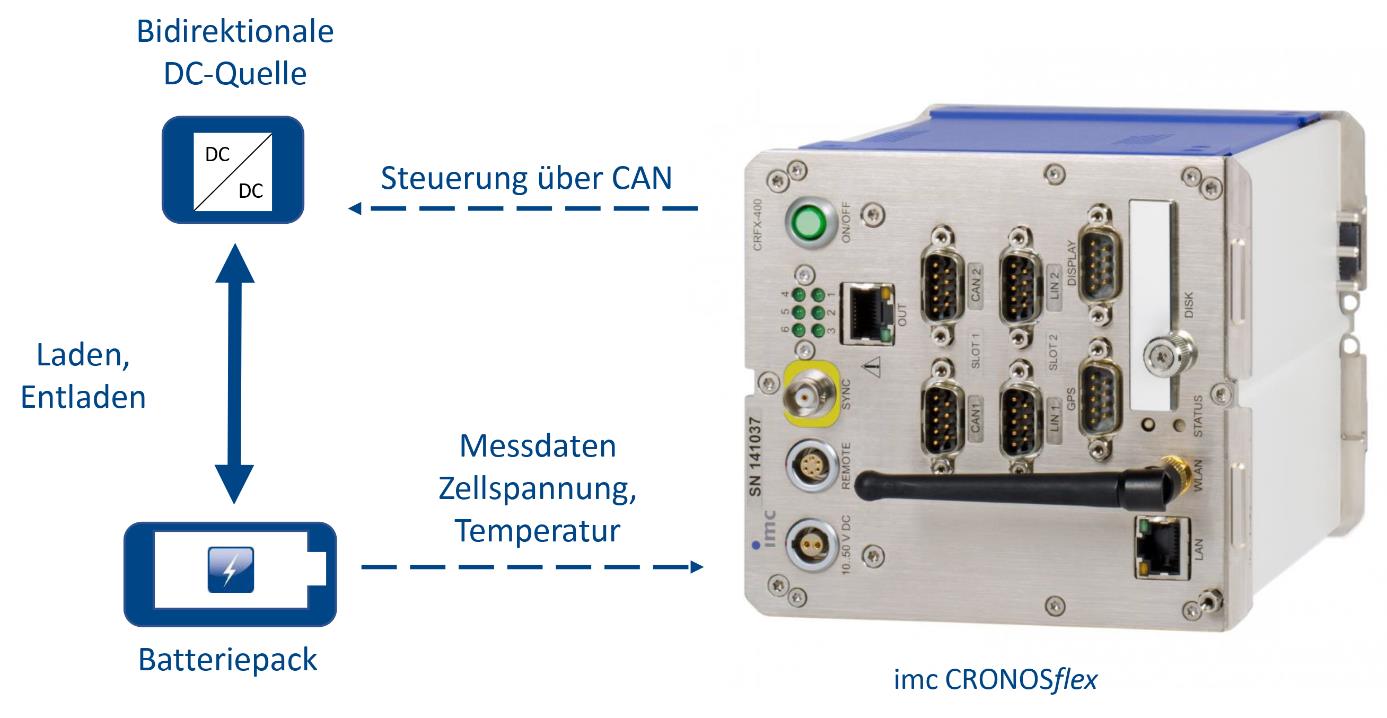
Lebensdauer- und Zerstörungstests
Die verschiedenen Batterietests dienen dazu, die Lebensdauer und die Zuverlässigkeit der E-Fahrzeugbatterie in verschiedenen Belas-tungssituationen, wie z. B. einem Unfall, zu si-mulieren. Tests mit Crash-, Penetrations-, Stauchungs- und Biegungsbelastung sollen Aufschluß über die Sicherheit eines Batterie-packs geben und sind durch Normen festge-legt.
Lithium Inonen Batterien benötigen für die hier angegebenen Tests die richtige Testumge-bung, da es durch die gezielte Zerstörung des Batteriesystems zum gefürchteten „thermi-schen Durchgehen“ kommt. Das Schmelzen des Seperators führt zu einer unkontrollierte Abgabe der gespeicherten Energie der Zellen. Durch den Sauerstoffgehalt in der Umgebung kann es zum Brand oder zur Explosion der Bat-teriezellen kommen.Die Testumgebung muss daher feuerfest und
explosionssicher ausgelegt werden bzw. Druckwellen müssen gezielt abgeleitet und entstehenden Schadstoffe dürfen nur gefiltert in die Atmosphäre gelangen.
Life cycle and destruction tests
The various battery tests are used to deter-mine the life cycle and reliability of the e-vehi-cle battery in different load situations, such as simulating an accident. Tests with crash, pene-tration, compression, and bending loads serve to provide information about the safety of a battery pack and are stipulated by standards. Lithium-ion batteries require the correct test environment for the tests specified here, as the targeted destruction of the battery system leads to the dreaded “thermal runaway”. The melting of the separator leads to an un-controlled release of the stored energy of the cells. The oxygen content in the environment can lead to a fire or an explosion of the battery cells. The test environment must be designed to be fire-proof and explosion-proof, or pressure waves must be diverted in a tar-geted manner and the pollutants produced may only be filtered into the atmosphere.
Penetration Load Test
When testing penetration load, the imc test system records the battery cell voltage. The temperature is recorded with a thermal imag-ing camera. A film camera documents 5 destruction. All images and measurement data are stored synchronously for evaluation.
Misuse- and crash-Test
A thermal imaging camera and a high-speed camera are used for dedicated mechanical de-formation tests on the battery pack (crash, compression, and bending loads). Here, too, the measurement data and camera images are stored synchronously.
Vibration-test
In the vibration test, the batteries are sub-jected to oscillations that occur during vehicle operation to analyze material loads on the sys-tem. A so-called “shaker” generates strong vi-brations, while the test system monitors the condition of the battery pack during charging and discharging.
Life cycle test in a climatic chamber
The life cycle test of a battery pack includes charging and discharging cycles over several weeks to test the performance of a battery. The battery pack is exposed to various de-grees of humidity and temperature profiles in a climatic chamber
Test stand control and data analysis with imc STUDIO
Based on imc STUDIO software, the test stand controller regulates the charging and dis-charge process of the bidirectional DC source in the various test environments using pro-cessed measurement quantities. It is also pos-sible to end the test, switch off the test, and control other test stand components. Other devices such as climate cabinets, shak-ers, and drives can be integrated into the test stand control via imc STUDIO. Measurement data is evaluated with imc FAMOS software. This allows analyzes to be carried out across different site locations to meet the high-qual-ity requirements of battery production.